First, the accumulator to absorb pressure pulsation effect of poor reasons
The accumulator's own parameters
Improper selection of capacity: If the accumulator capacity is too small, can not store enough pressure fluctuations in energy, it is difficult to effectively absorb the pressure pulsation; while the capacity is too large, it will lead to slow response, also affect the absorption effect. In the hydraulic pump displacement, high frequency of pressure pulsations in the system, if the accumulator capacity is insufficient, the absorption effect will be greatly reduced.
Precharge pressure setting error: precharge pressure is too high or too low, will destroy the balance between the accumulator and the system pressure pulsation. Precharge pressure is too high, the ability of the accumulator to absorb pressure pulsations is limited; precharge pressure is too low, the accumulator in the normal fluctuations in system pressure premature emptying, can not continue to play a role.
Damage to the bladder or diaphragm: In bladder or diaphragm accumulators, the bladder or diaphragm is the key component. Once there is a breakage or aging, it will lead to the mixing of gas and liquid inside the accumulator, affecting the normal work of the accumulator and reducing the absorption performance of pressure pulsation.
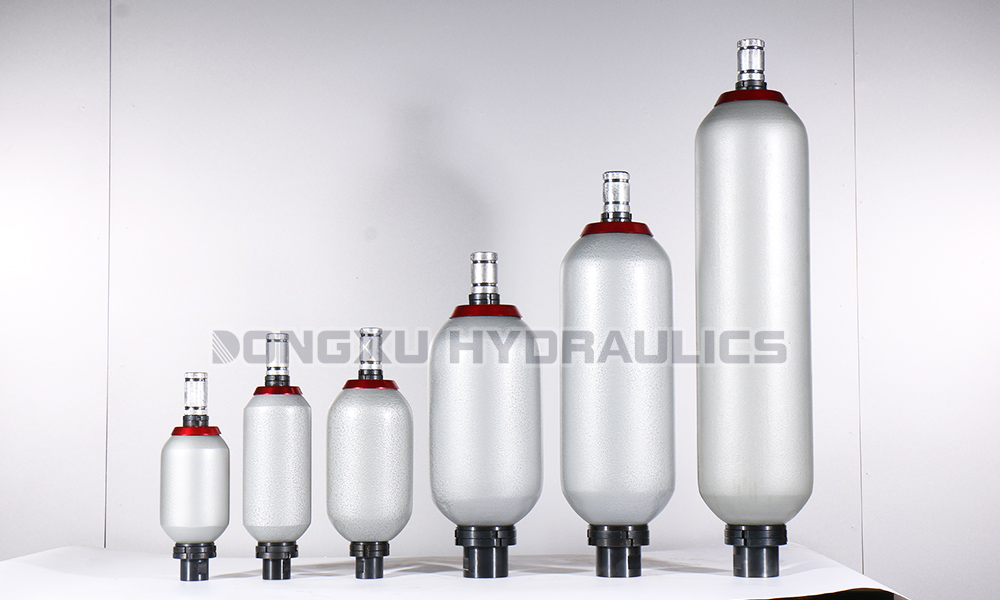
System matching problems
Installation position is unreasonable: accumulator installation position is too far away from the pressure pulsation source, will make the pressure pulsation in the transmission process attenuation, while delaying the response time of the accumulator, resulting in poor absorption effect. For example, in the hydraulic system, if the accumulator is installed in a position far away from the hydraulic pump, the pressure pulsation can not be absorbed in time.
Piping design defects: piping is too long, too thin or too much bending, will increase the resistance to fluid flow, resulting in pressure loss, weakening the accumulator on the pressure pulsation absorption effect. In addition, the rigidity of the pipeline is not enough to produce vibration under the action of pressure pulsation, will also interfere with the normal work of the accumulator.
Poor synergy with other components: accumulators and the system of hydraulic pumps, valves, filters and other components with poor coordination, will lead to system pressure fluctuations in disorder. When the flow pulsation frequency of the hydraulic pump is similar to the intrinsic frequency of the accumulator, resonance may be triggered, exacerbating the pressure pulsation.
The working environment and maintenance issues
Fluid contamination: The fluid in the hydraulic system, if it contains impurities, water or oxidative deterioration, will affect the sealing performance and hydrodynamic properties within the accumulator, resulting in a decrease in the ability to absorb pressure pulsations. Impurities may also wear out the skin capsule or diaphragm, resulting in leakage.
Temperature effects: High or low ambient temperatures can have an effect on the performance of the accumulator. Too high a temperature will make the gas expansion, reducing the effective volume of the accumulator; too low a temperature will make the oil viscosity increases, affecting the flow of fluids and the response speed of the accumulator.
Lack of regular maintenance: Long-term failure to check the accumulator's precharge pressure, skin bladder status and fluid quality, unable to detect and solve potential problems in a timely manner, resulting in a gradual decline in the performance of the accumulator, the effect of absorbing pressure pulsations deteriorated.
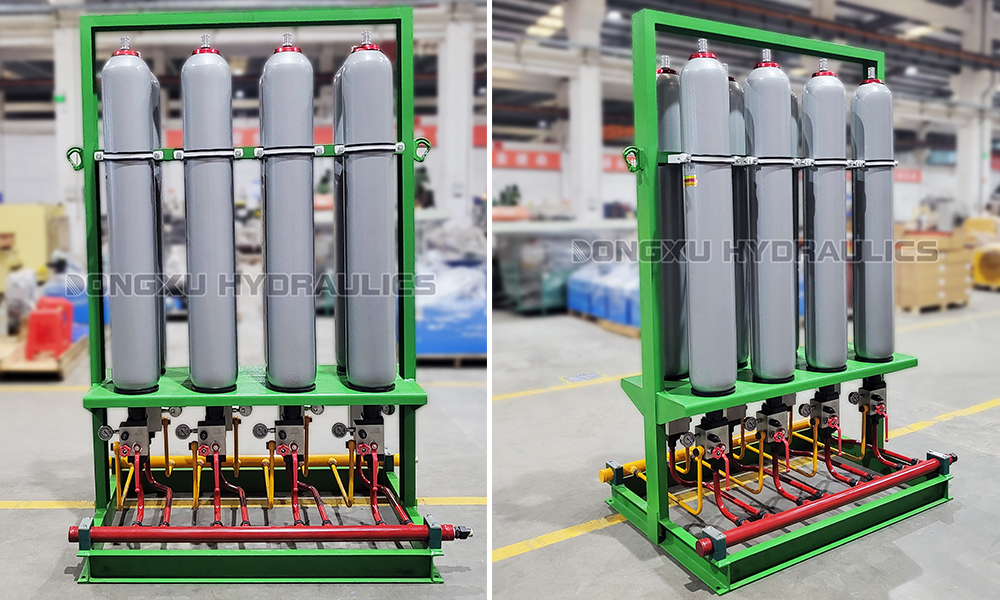
Solutions
Optimise accumulator parameters
Reasonable selection: according to the system flow, pressure, pressure pulsation frequency and other parameters, accurate calculation of the required accumulator capacity. Through the theoretical formula combined with the actual working conditions test, select the appropriate capacity of the accumulator to ensure that it can effectively absorb the pressure pulsation.
Correctly set the precharge pressure: Refer to the instruction manual of the accumulator and the working requirements of the system, and use professional filling equipment to set the precharge pressure within the appropriate range. Regularly check the pre-filling pressure and adjust it in time if any abnormality is found.
Replacement of damaged parts: If the skin bladder or diaphragm is damaged, it should be replaced with new parts immediately. Choose reliable quality bladders or diaphragms that match the accumulator model to ensure proper installation and avoid leakage.
Improve system design and installation
Adjust the installation position: Install the accumulator as close as possible to the pressure pulsation source to reduce the pressure pulsation transmission distance and improve the response speed. At the same time, ensure that the installation is firm to avoid vibration affecting the performance of the accumulator.
Optimise piping design: shorten the length of the piping, reduce unnecessary bends and joints, choose the right diameter of the pipe, and reduce the resistance to fluid flow. Increase the rigid support of the pipeline to reduce vibration. For long pipelines, consider the use of accumulators in series or the addition of buffer devices to improve the pressure pulsation absorption effect.
Improve component synergy: In the system design stage, give full consideration to the matching between the components. Adjust the working parameters of the hydraulic pump to avoid resonance with the accumulator; reasonable arrangement of valves and filters to optimise the fluid flow path and reduce pressure fluctuations.
Strengthening the management and maintenance of the working environment
Purify the fluid: replace the hydraulic oil regularly, use high-quality filters to filter impurities and water in the fluid. The establishment of a fluid monitoring system, regular testing of the cleanliness and physical and chemical properties of the fluid, found that the problem is handled in a timely manner.
Control of operating temperature: to provide the accumulator and the hydraulic system with a suitable working environment temperature, can be adjusted through the installation of cooling devices or heating devices to regulate the temperature. Avoid accumulators working under extreme temperature conditions to ensure its stable performance.
Regular maintenance: Make a detailed accumulator maintenance plan, regularly check the precharge pressure, skin bag status, fluid quality, etc.. Clean the dust and oil on the surface of the accumulator in time, check whether the connection parts are loose to ensure the normal operation of the accumulator.